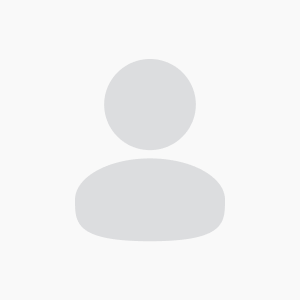
William Pankiw
Forum Replies Created
-
William Pankiw
MemberNovember 28, 2022 at 11:23 am in reply to: Flat Rate isn’t dead yet, but it’s getting sicker and may not recoverI have used a high paycheck paid bi-weekly with a bonus paid monthly for 25 years. I review it every 6 months, and adjust it based on sales. None of my Technicians work (are on the property) over 40 hours, do not work nights or week ends. Works for me.
Bill
-
William Pankiw
MemberMarch 14, 2022 at 6:51 pm in reply to: 10 Rules For Selling Your Transmission Shop (or any shop for that matter)So…Where can one find “At a minimum, you should be looking to hire someone who has had experience in selling auto repair businesses and who can persuade you that they can “walk the walk and talk the talk” of why your business is a great opportunity.” I’ve looked everywhere and I can not find even a listing in all of Chicagoland for an Automotive Business Broker that has credentials, and verifiable sales. I would Love to have any referrals any member has, good or bad.
-
I do this as well every January with my Service Manager, Shop Foreman, and every Technician. We just purchased 2 new Scanners from Snap On to compliment our Shop Key management program, 1 being a new Pro Link scanner for Isuzu and Hino. When my Shop Foreman stated “We should get a new Sledge Hammer before someone kills them self’s”, I was floored, I never knew nor do I use it, so we purchased a new Wilton 16LB. 1 piece on Amazon, cheap insurance. As the old saying goes, “You don’t get unless you ask” I wish Great success to everyone in 2022.
Bill Pankiw
-
William Pankiw
MemberJanuary 10, 2022 at 2:03 pm in reply to: Unpaid Days or Time Off Policy – New Document in the Premium Member AreaNothing shows up under unpaid time off, am I missing somethin here?
Bill
-
Repairlinkshop.com has now given us an outlet to look up and ordering most all OEM parts through our participating dealers, but as we have found, their cataloging is not always correct even looking everything up by VIN. Auto / Truck repair has never been an exact science and NEVER will be..
-
William Pankiw
MemberOctober 29, 2021 at 10:52 am in reply to: Parts shortages and backorder questions and what we are doingBrake parts are a real challenge, tires are impossible as well. We have been telling all customers and fleet management companies 24 hours on price quotes since early July when we got our first major price increase on brake parts. We currently are in need of a 6.8 liter V-10 engine for a 2014 F-450 and were told 3 – 4 months for delivery through Ford. AER, the company that rebuilds engines for Ford is said to have a $3,000,000 back order on parts. Jasper had 1 in the country and when we went to get it is was $1600.00 more our cost. Then next day it was gone. At that point Jasper told us 6 -8 weeks Projected ? delivery. I was able to get an engine coming from our Ford dealer in 7 – 10 days through an emergency order that was placed in early September for someone else. It is suppose to be here 11/5/2021. We’ll see.
With new vehicles / Cabs and chassis for commercial vehicles being in short supply, we are seeing companies repairing vehicle they would normally replace so this problem is only going to get worse in my opinion. Bill
-
William Pankiw
MemberDecember 7, 2020 at 6:41 pm in reply to: November 2020 Sales at Your Shop – Up? Down?Nov -20%
-
William Pankiw
MemberApril 15, 2019 at 8:20 pm in reply to: Assistant service manager – Position Open in Elk Grove, IllinoisDoes anyone have a comment or an idea on marketing for an assistant service manager? I have done the Career Builder and Indeed routes with no success.
-
X3 with Tom
With the fast pace of my shop, we can not risk the hassle of letting a counter guy order the parts we need. Everything is VIN driven on most all of our supplier’s web sites (Except the OEM Dealers). And sites like Motorcraft have VIN filters to help narrow down getting the correct part. As far as calipers, that is like a revolving door with every supplier we have used. I just had a meeting last week with the national sales manager of a large supplier with no real answers to all the problems we are seeing. So I left him with “Sounds like a YOU problem” and are now once again trying some other suppliers. The quality of remanufactured parts in our industry is just pitiful, the only thing consistent, is the inconsistency of the quality.
-
I have been a Master Certified Technician since the early 80’s (?) when it was called the NAISE before ASE, back when we were called “Mechanics”. I have re-certified every 5 years as required. My shop has been a Blue Seal Certified shop since it’s inception, and is the only one in our Zip code of 35,000 people. I believe you can not require your Staff to be Certified in the ASE unless you show by example, be it a Service writer , Apprentice, or Technician.
I have not been “Hands On” in my shop for the last 33 years, and I have no problem passing all 8 re-certifications by keeping up with technology. I believe you are either In or Out when it comes to this PROFESSION. Those who complain about ASE testing being hard are just not committed. If your performing all the work correctly on a daily basis, you should pass any test related to your job.
-
William Pankiw
MemberMay 23, 2018 at 6:43 pm in reply to: Has Anyone Found a Tech Using One of These 17 Companies?No. I gave up years ago using the above listed services. . I “Breed” my own from Automotive Tech Schools or College Automotive students that are paying tuition to be there. This way they have a vested interest. It’s just hard to get them to put their phone down (they look EVERYTHING up on Google)
Bill
-
I am on my 4th Hunter Machine in 38 years and would have nothing else. Every machine I had prior is still in operation to the best of my knowledge. We average 5 – 7 alignments a day