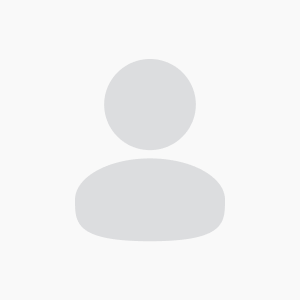
jerseysure
Forum Replies Created
-
jerseysure
MemberAugust 4, 2016 at 5:53 pm in reply to: I can buy the parts online alot cheaper !!!!!!!! Thoughts ?I don’t own the store I work at, but have been here 18 years and after so many examples of installing customer parts gone wrong, I personally will not agree to it. If the owner over rides me, so be it, he can deal with it. Although we are a family owned business, we sell Goodyear tires, so the easiest response with the least push-back is “I’m sorry, we don’t install customer supplied parts as per our agreement with Goodyear’s nationwide warranty program..”. Quite literally almost every time I had made an exception, it back fired in one way or another, the most aggravating being when they complain about the labor price after the fact. As someone stated here, they are generally a “special” type of customer, not one that I want. Look, I’ll still install an established customer’s light bulb or wiper blade that they thought they could do themselves, but that’s about it.
Dennis
-
Almost every sales book, seminar, what-have-you I’ve read and been to in my 20 years doing this has said that you have to truly believe in what you are selling. I am a true believer in changing fluids. I do it on my own vehicles, my family and friend’s vehicles, and enjoy maintaining safe, reliable vehicles that run and drive like new after 10 years on the road. I wouldn’t enjoy driving around in a poorly maintained junker, no matter how little I can brag about spending on it. I just leased my first vehicle, a 2015 Sierra Denali, and even as a lease, I don’t let the oil monitor dictate when I change it. I won’t exceed 5000 locally driven miles, even with full synthetic. I just can’t do it. It looks gross at 5000 miles and I take it pretty easy and use top-tier fuel. We replace — honestly — twice the amount of engines and transmissions than we used to–many at or just below 100k miles. I won’t complain that people aren’t maintaining their vehicles-it has been very lucrative for us. However, i will suggest they do when in for service–nothing set in stone, my suggestions vary from manufacturer to manufacturer, and there are some european vehicles I won’t even pretend to know what’s right because it’s just not in my wheelhouse. I honestly feel I am doing the right thing when changing vital fluids-I am helping someone maintain a high-value vehicle. The manufacturer’s recommendation(s) mean little or nothing to me – they can’t change what I see here every day.
On the subject of AAA–their motivation is very different from mine. Their company owned stores are purely gross-profit driven, fluid-flushing filter-brake-tire changing machines. Every low-buck, free tire rotation car gets a full blown fluid analysis and inspection every time (most often by a poorly trained or inexperienced general service tech). Their playbook is almost word-for-word that of “Mr. Tire”, another chain that focuses on baiting people in with low dollar coupons and beats them over the head when they get there. AAA has a unique advantage as the company has over 100 years of trust with a huge customer base they can access; but I truly believe most people that take the bait quickly regret the decision. Yes, pretty shop, good face value. However, with little or no talent in the shop and people getting crushed with their ridiculous parts mark up matrix and three stooges style process many shops need not worry. Call them for a quote on anything–tires, brakes, whatever. I believe you’ll have your mind put at ease pretty quickly. Go in and watch the shop for a half hour. Listen to the customers waiting for their cars. It will make you proud of what you do. Anyone good they get to run the stores or work in the shop don’t stay too long. (I’m sure there are some exceptions–I only know about what I’ve seen, experienced, and people I know who worked there in my area in NJ)
Dennis
-
Installing customer’s parts has gone south on me 95% of the time. I just won’t do it anymore. I don’t feel I deserve the added stress or liability that comes with it. We are busy enough with people that allow us to conduct business the way we need to. When customer’s ask, I tell them I won’t do it and refer them to the owner. He hates not taking $ so he sometimes allows it. When a problem arises (which it often does), I direct them to the owner. No stress on me. I try and do the right thing the best I can every day, and I don’t think installing customer supplied parts is the right thing for anyone.
-
Free (hot) air all day long. 7/10 times results in repair or replacement of a tire or TPMS related component.
-
We use both, although here it my perception of IATN.. On IATN you must contribute by posted fixes or help. Therefore, often times when I post a problem, I get half a dozen responses or more that either make little or no sense, or ask me questions that are easily answered by reading my post. For example we recently had a very very stubborn steering problem with a Honda. I had posted all the things we had already done. I had posted we used Honda OE fluid. The first several responses were “Hey, did you change the resovoir, there’s a TSB about that.” Yep, did that..see post. “These cars are picky, you MUST use OE Honda fluid.” Yep. Did that. Read post. Obviously I don’t respond in a snarky manner but c’mon most of us by the time we post on one of those boards we’ve gone thru TSB’s and made sure we’ve crossed all the t’s and dotted the i’s. My point is I think on IATN people post “help” for the sake of posting and getting their requirements met. Just my guess, could be wrong.
Dennis
-
We stick to one labor guide, it has treated us well. Maybe a handful of times it seemed high or low, win some lose some.. never had an instance where it was so far off that it hurt us. In the case you mentioned I would have done a little research on the R+R procedure and decided which was most accurate/fair to both the customer and the shop. We had one recently, some front hubs in a Toyota pickup. We told the customer the job calls for nearly 7 hours according to our guide, although we weren’t sure why. With that being said we quoted him the 7 hours plus parts, and told him if the guide was way off we’d do the right thing and collect less. Well the guide wasn’t wrong–it sucked, and took a good part of the day..
-
jerseysure
MemberJune 2, 2014 at 12:25 pm in reply to: Input Needed – What is your Standard Warranty?2 year/24K nationwide out here..
Dennis
-
If they clock in/out for 48 hours (they are in the building “working” for 48 hours), their flag hours should be at least 38.4 hours for 80% productivity (48 multiplied by .80) (although any good tech would probably crank out 60+ hours in a shop with good car count and salesmen/advisors). The way I look at it is if you worked 48 hours, you should want to get paid for 48 hours or more.. Therefore the shop I am in now, being very busy, I constantly monitor my tech’s billed labor hours and let them know where they are at for the week. It gets them rev’d up when they are ahead of the game and they can expect a good check. Keeps them off their phones and focused on efficiency.
I have one tech who was consistently producing 60+ hours per week, working 48 (really working 44 if you take his lunchbreaks out).I moved him to a nice hourly rate because he was having trouble getting a mortgage with the incentive based flat rate system. They wanted a steady hourly income.His productivity is now at 30-40 hours per week. Now that his pay is guaranteed regardless of what he does, he doesn’t hustle. He smokes more, bs’s with others.. basic human nature man.I’ve discussed it with him several times but he doesn’;t see it that way. He’s got excuses for everything. He is a very good tech so I will figure something out but it’s looking like he will be back on flat rate soon. I tried to help him out with this but he is producing 1/2 of what he used to.Dennis -
Well if they are jacking around and goofing off then they aren’t making money for themselves or you. When I was at a corporate facility the guys had to have an 80% or better productivity rate or progressive discipline would begin. You need to let these guys know your expectations if you haven’t already. Guys that are willing to learn and seem interested when you explain the business side of things are worth your time. Others can goof themselves out of a job when they are on the clock for 48 hours and get paid for 20. I’ve had many flat rate guys that wanted to be handed everything–never worked for it–never checked cars out. Slowly those 20 hour paychecks took their toll, the good guys/producers would find legit work and obviously I would feed them in return. They always whined they weren’t getting “good work” and eventually quit. Took a few months but being corporate it was easier than going thru “prog discipline”.
-
I’m guessing they are paid hourly regardless of productivity?
-
That all depends on a lot. Old dogs that can’t/wont be taught new tricks? Younger and inexperienced? Older and inexperienced? Does anyone have the will to learn or increase their skills? My biggest obstacle lately is the aging tech (57) who will gladly tell you “He’s forgotten more than most guys know” and was great back in the day but fails to accept that his body, eyesight, hearing, and failure to learn new technologies and procedures is pushing him right out of a job. Low productivity, missing things, diagnosis way off– luckily have others to carry him but he can’t do this much longer..
Most young guys in my experience have to “want” to do this. Otherwise it’s a waste to invest in them.Dennis -
The sign-offs are great in theory but I believe most techs pencil whip them and don’t actually double-check. I had a verbal drain plug check in place which I thought was very effective “drain plug tight” “OK” but found that when management wasn’t around they wouldn’t do it and just jot some initials down on the RO.
Being a very high volume shop I have had the unfortunate experience of dealing with an oil filter coming off, a drain plug or 2, and more wheel-offs/loose wheels than I’d like to admit (mostly due to corrosion/not seating properly–not being left loose–but result is the same).In every case, my employee was extremely upset at what happened. They didn’t immediately take the “I didn’t do it” course, you can tell right away they feel terrible and almost can’t believe it happened. They know not to get defensive, and many times have had to go help a customer on the road with their tail between their legs which is terrifying if you’re not used to dealing with the public every day face-to-face.Everyone makes mistakes. I never minimilize it like that to the customer unless they are getting out of line. I tell them I’m sorry, it’s a terrible mistake to make, but it’s a mistake and we will make it right. I usually give myself time to calm down from the stress of the situation then talk to my employee the next day–usually taking the approach of “we all make mistakes, but we can’t make one of these again.. you work on XX amount of cars a day and have had thousands come and go without incident–so I’m sure this is a one-time event”. All of my employees have been here 10+ years.Every situation is different–you have to look at the employee’s value and history. I know at least in my area, good help in this business is REAL hard to find..Dennis -
Same thing I do.. I will pull a code with a $300 launch for free. I reveal the code, explain a few possibilities, and secure diagnostic time to pinpoint the problem. The customers often appreciate that they are not being charged “to hook up the computer” so to speak. Obviously most people believe we plug in a computer and it simply tells us what to fix. If I get a large evap leak and the customer seems nervous from the get-go, I may offer to tighten the gas cap, clear the code and have him/her return if/when the light comes back for diagnosis. I feel like the few minutes spent helps secure the job or return business.