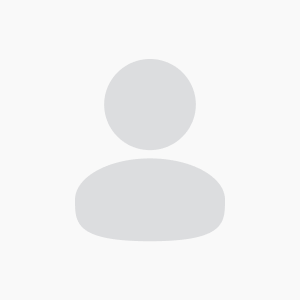
martin-zimmerman-us-bosch-com
Forum Replies Created
-
martin-zimmerman-us-bosch-com
MemberFebruary 3, 2014 at 8:24 am in reply to: How to manage cars waiting for parts cars waiting for payment etcI call on Automotive repair shops. The number of different ways that this process is accomplished changes with each shop I visit.
Using the color codes works well. White boards with catagories, etc. Nice and easy to see at a glance how your day is going.
Using a PC Software package also works well. This can be done with just the service writer or usually in a large shop with input from the technicians. Input from the technicians, over a network, is usually given some restrictions. I have a few shops where the tech’s use their PC input as a time clock, order their own parts, etc.
Multiple options for you. My suggestion is to do this at first, away from the daily grind. Decide what you want to do first, then try it alongside your current operation(as in a week or so) before fully implementing it. Also when deciding to make a major change like this, do it when your business is (relatively) slow. You need time to think clearly while these changes are taking place.
-
martin-zimmerman-us-bosch-com
MemberDecember 9, 2013 at 8:44 am in reply to: What I can do when my workers don’t want to?Technicians are best when they like and enjoy the technical challenges of vehicles. It does not matter if the vehicle is a car, tractor, school bus, etc. They need to want to get into the new technical changes that happen. I work for a very technically oriented Corporation, but the changes in vehicles not limited. Electronics, mechanical, drive types, etc. have happened already and will continue to happen. The best reponse for a technician is “Cool, look what they did this time!” as opposed to “Rats! why did they change this? The old way always worked!”. You, as the owner, need to find and develop this. Learning is a necessity in any business.